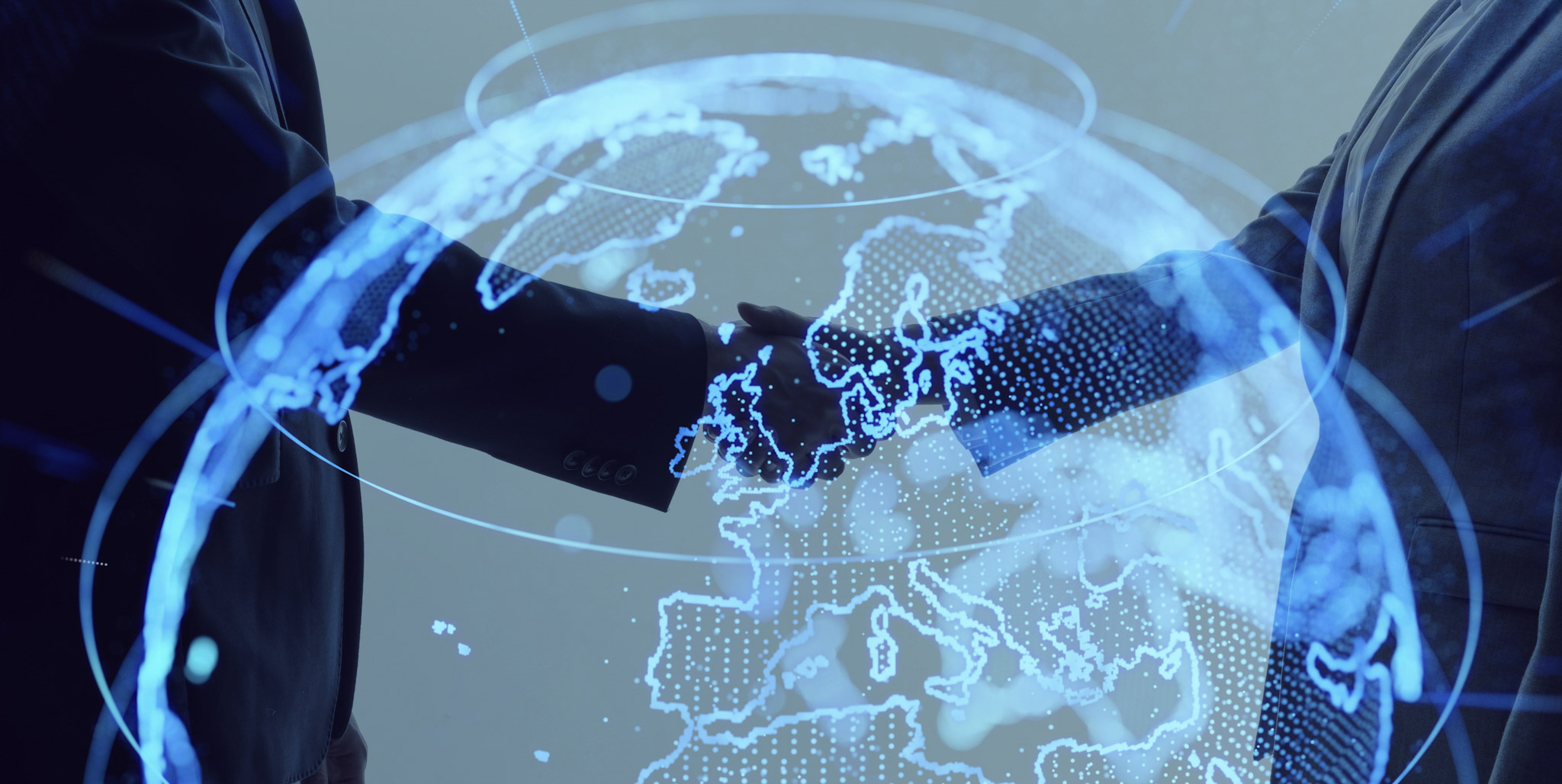
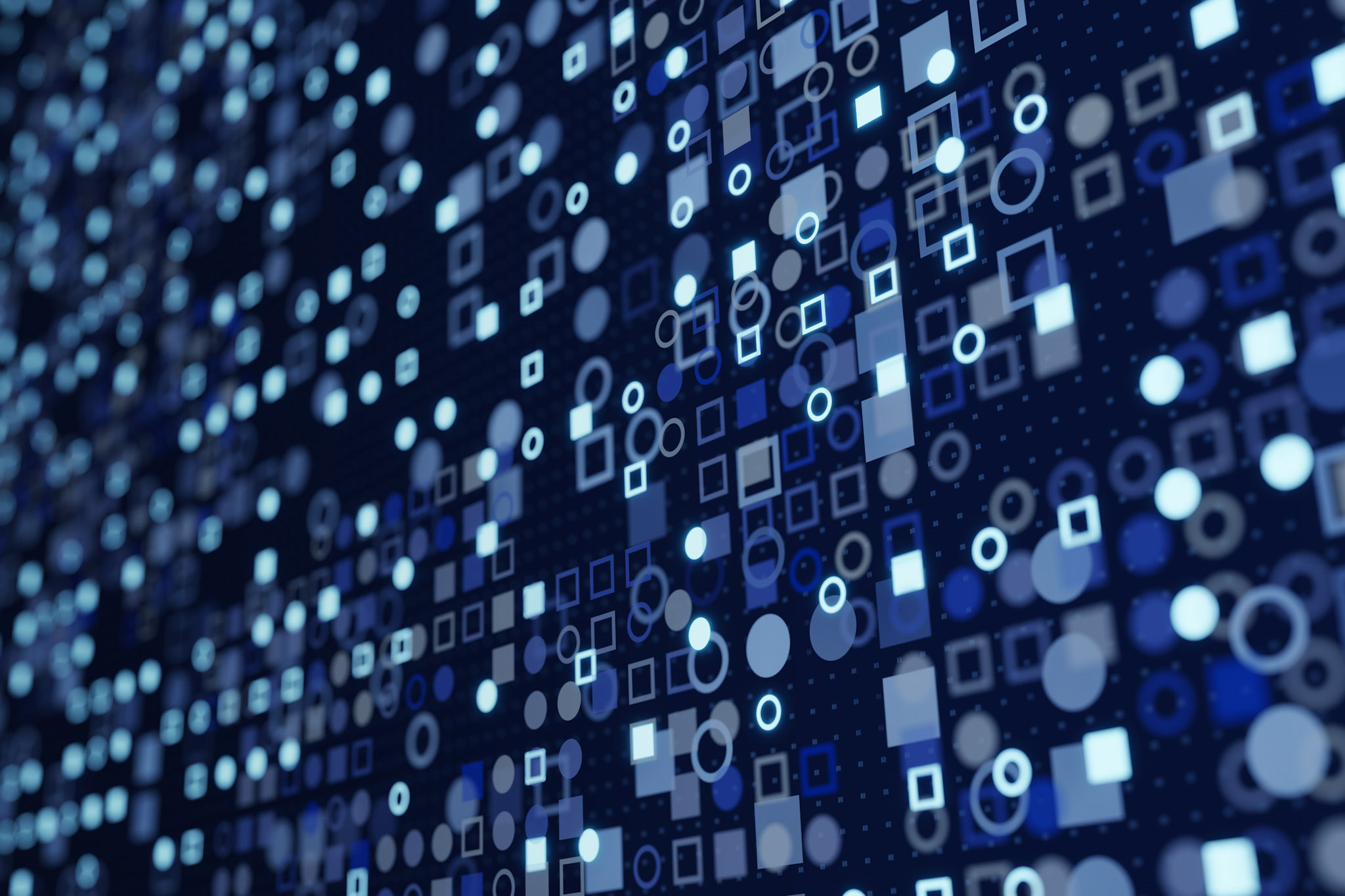
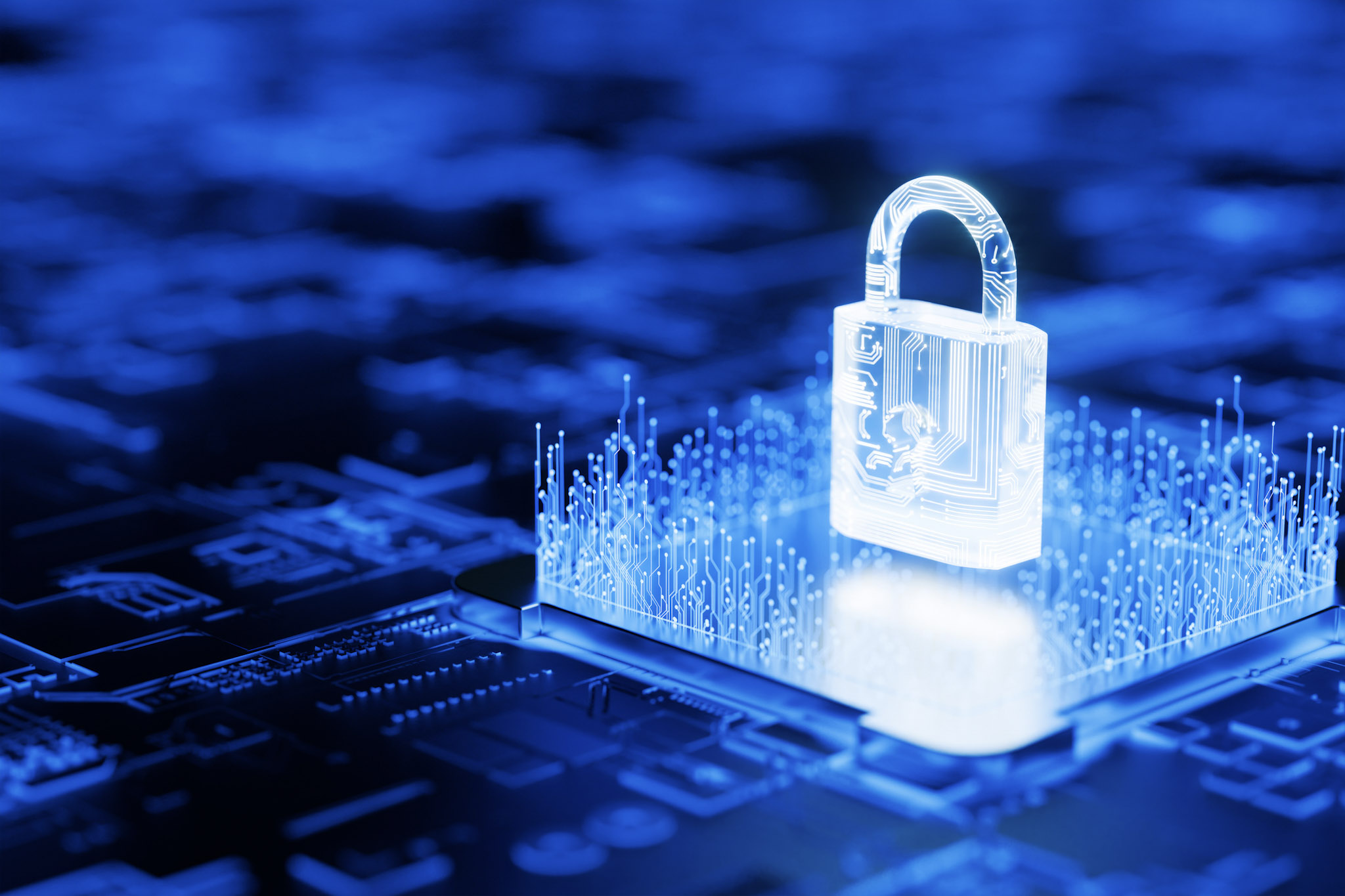

Trust in the Cloud: Building Transparent Data Relationships in Europe
The promise that European data stays within European borders is crumbl...
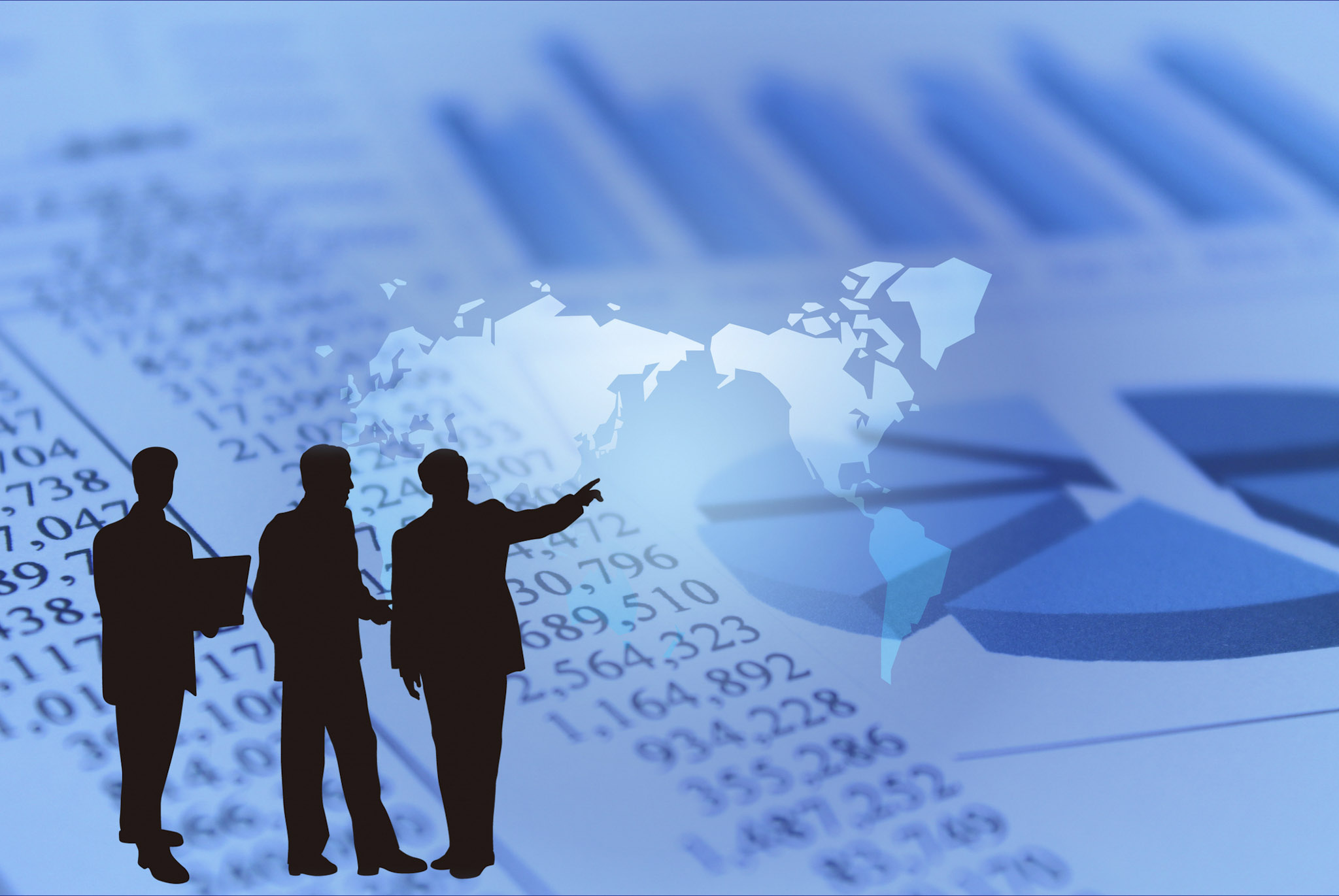
Finally Released – VCF 9 and the Comeback of Private Cloud (Light Edition)
Remember when we were all told, “Everything is moving to public cloud,...
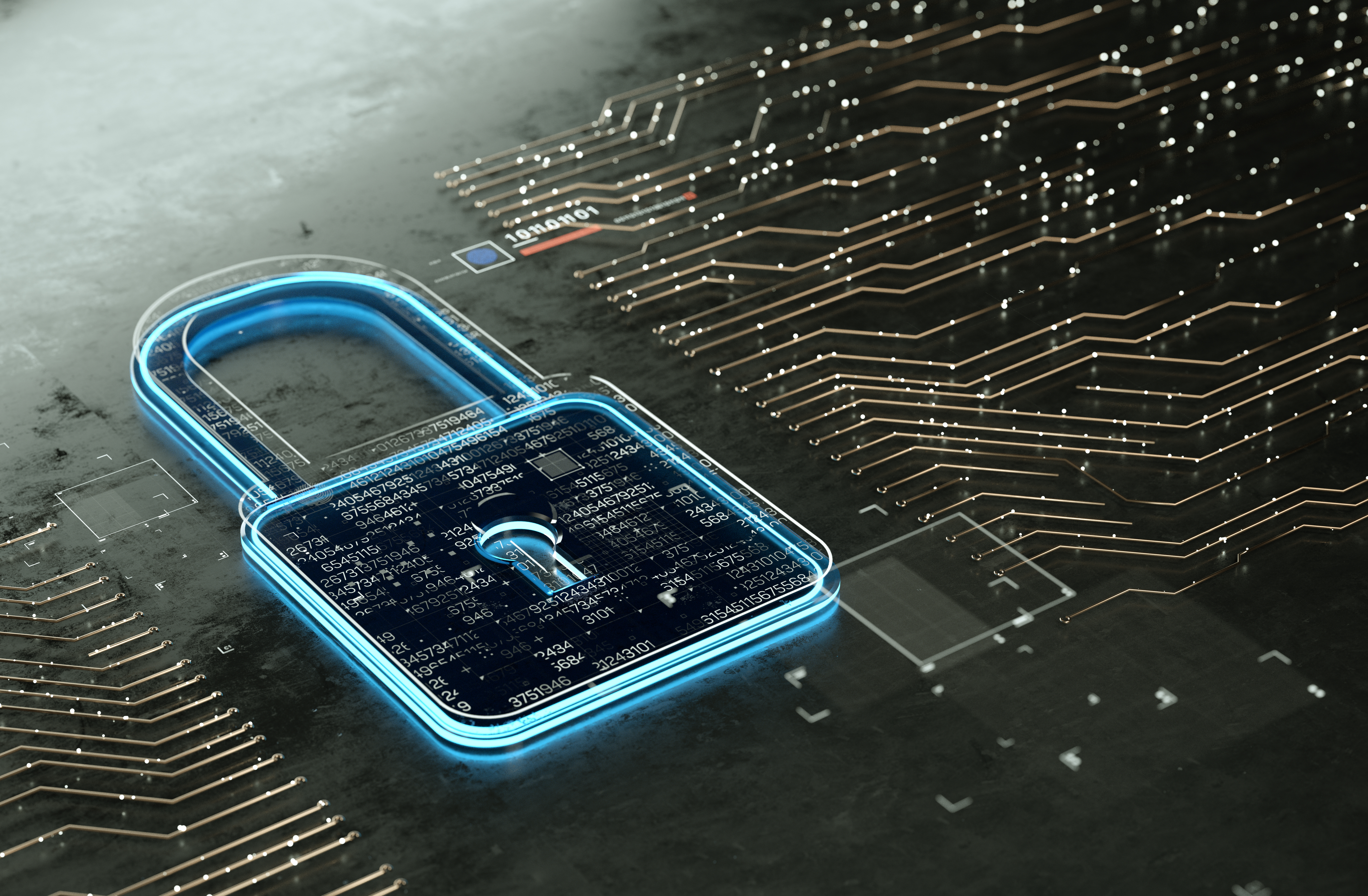
The future of AI is sovereign: Why data sovereignty is the key to AI innovation
The rapid acceleration of AI has brought countless opportunities, yet ...
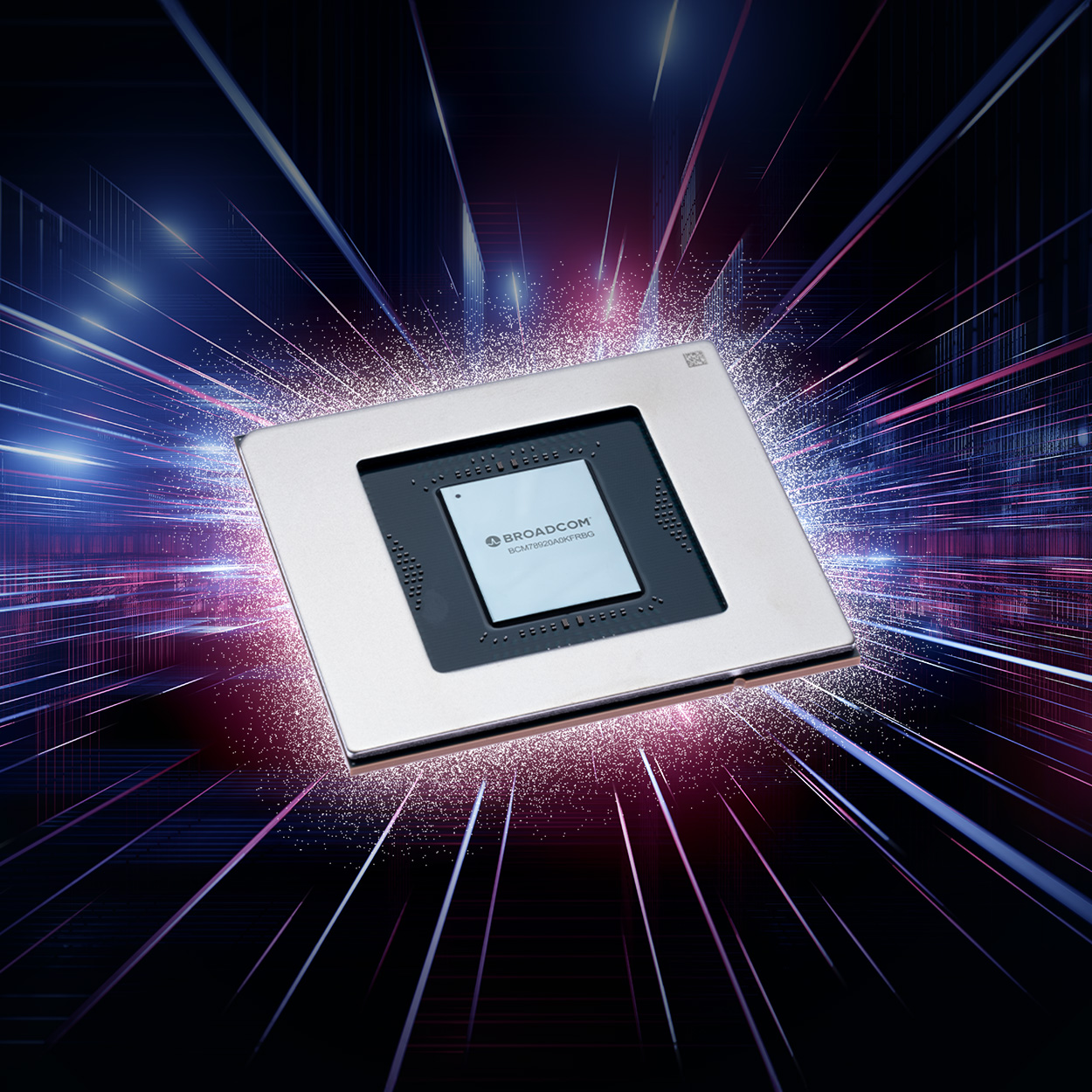
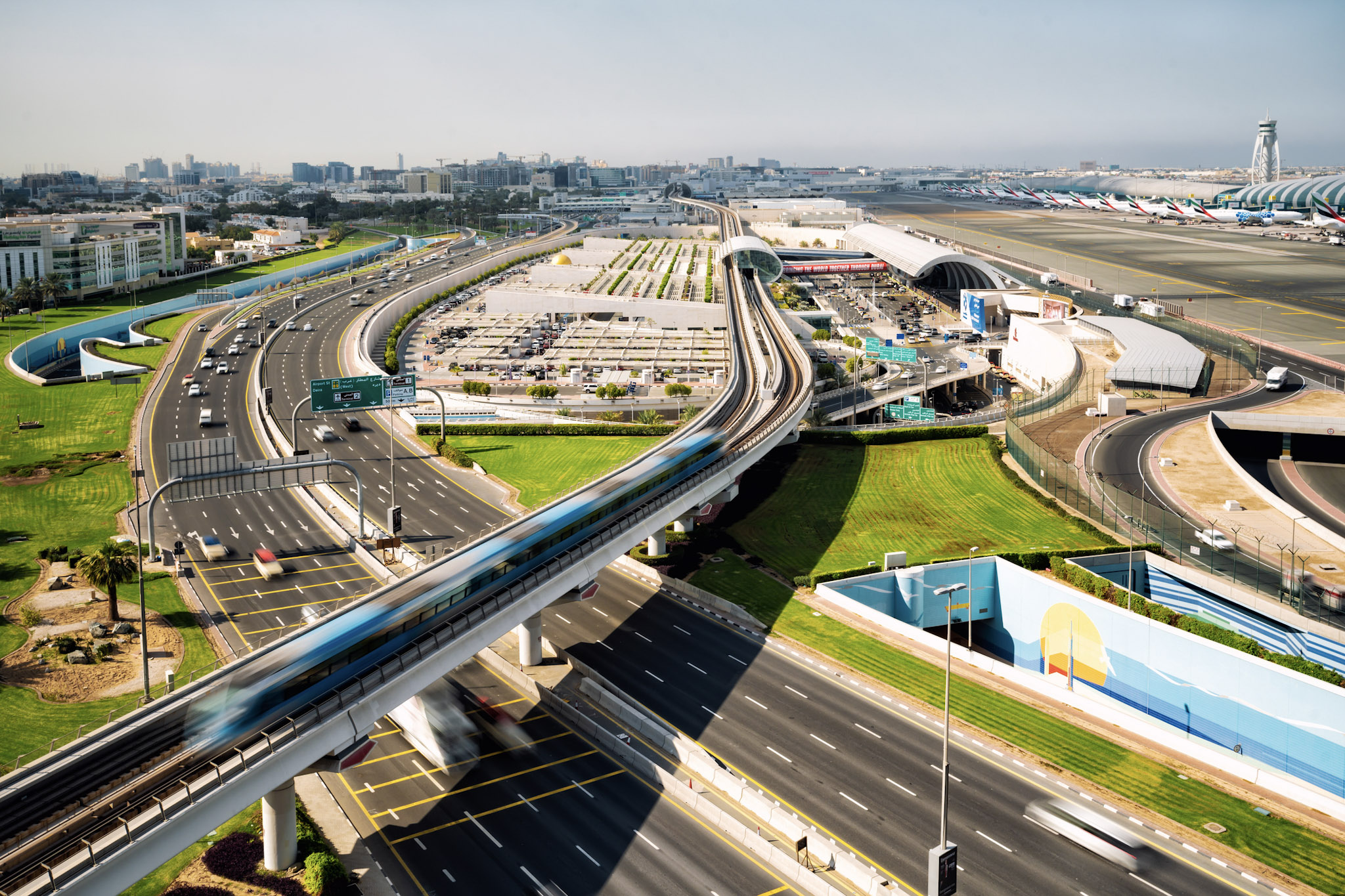
Dubai Airports Elevates Operations with Broadcom Software Solutions
Dubai Airports, operator of Dubai International (DXB), the world’s top...
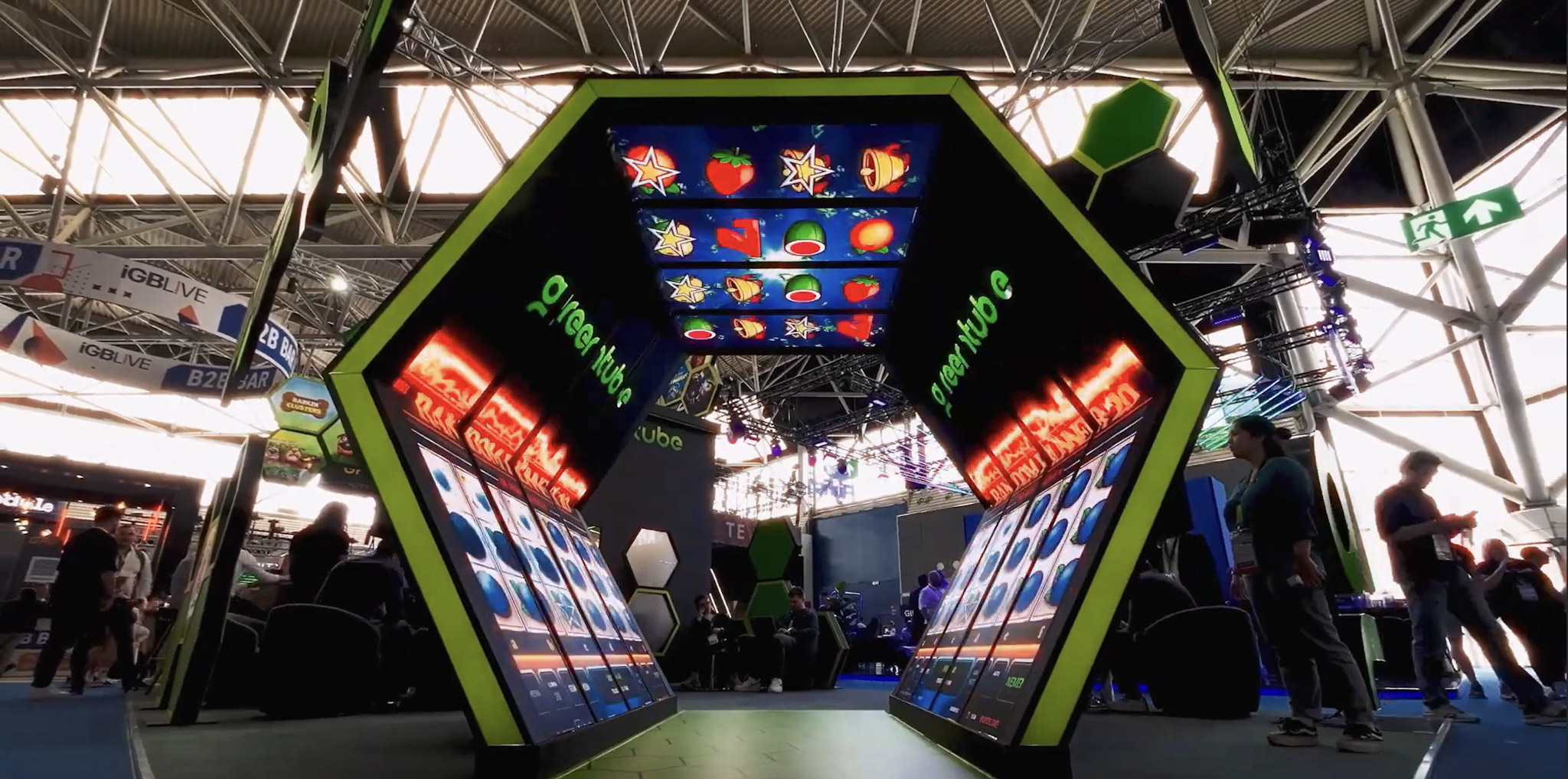
Leading Online Gaming Provider Greentube Overcomes the Challenge of Compliant, Global Expansion with VMware Cloud Foundation
The online gaming industry is booming. With over 1.2 billion projected...
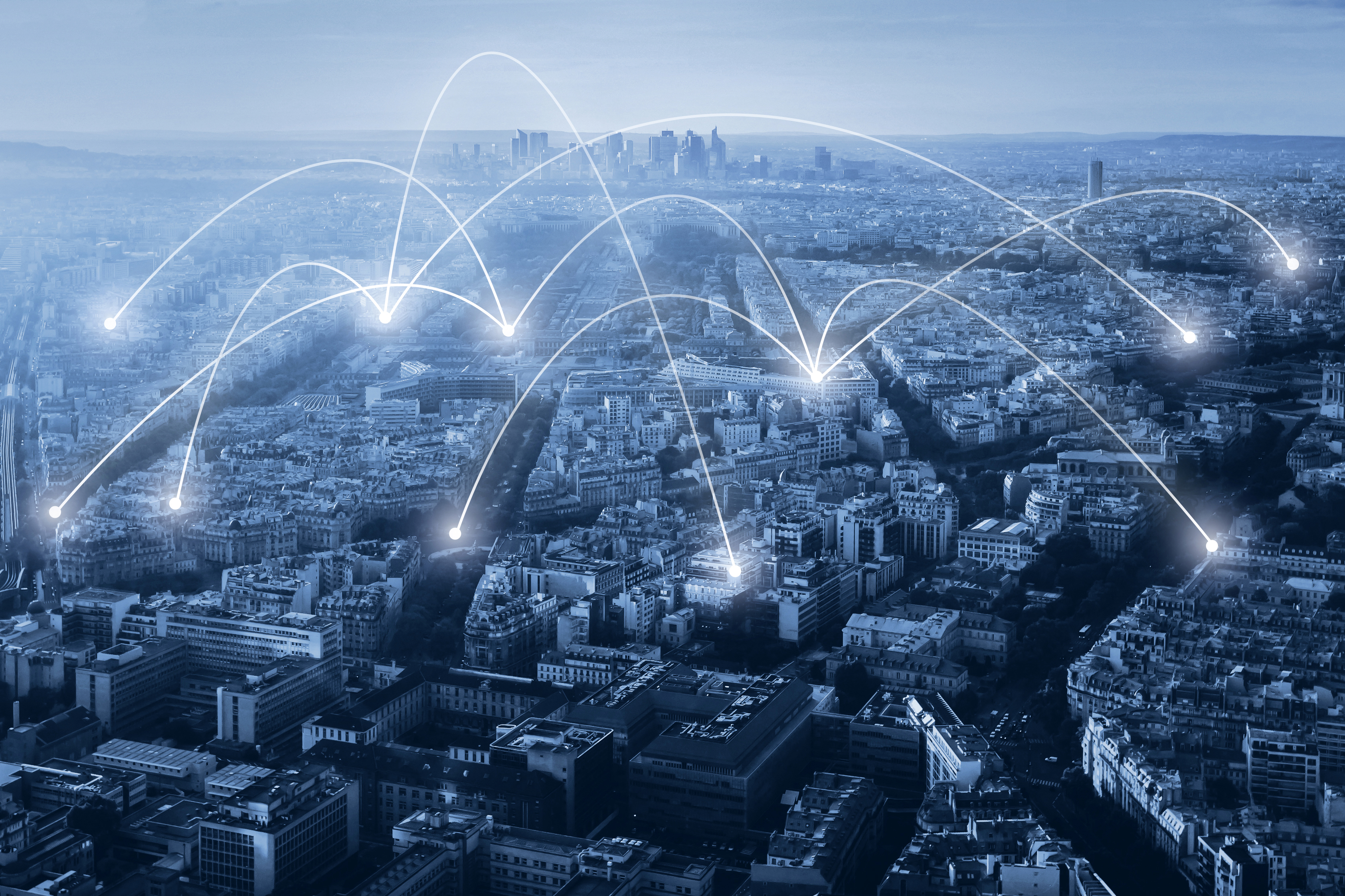
Bouygues Telecom renews partnership with Broadcom to accelerate its IT transformation and scale up its private cloud
Bouygues Telecom, a French all-round operator of digital communication...
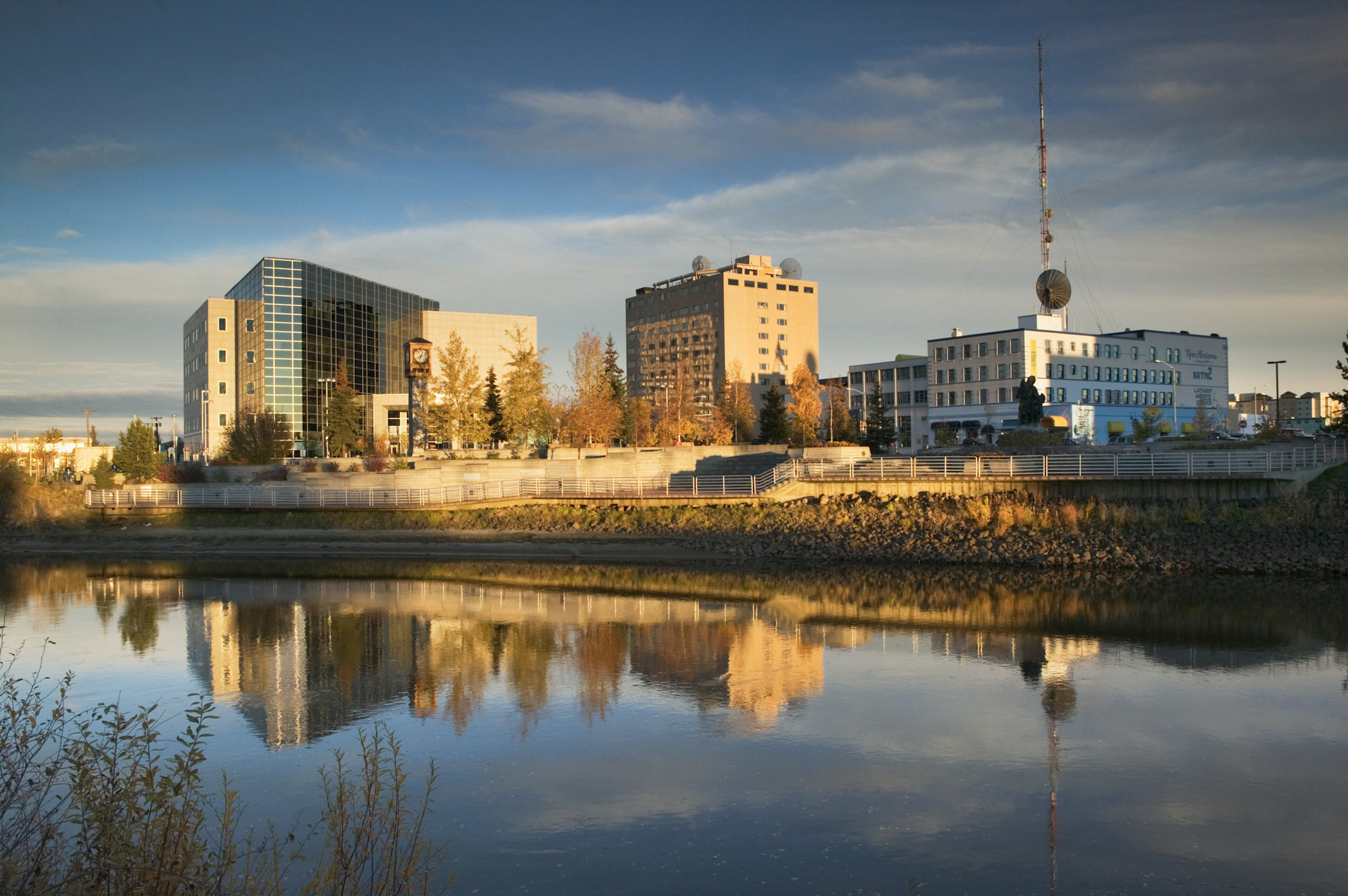
Broadcom Helps GCI Transform Operations and Services on the Alaskan Frontier
As the largest telecommunications company in the nation’s largest stat...
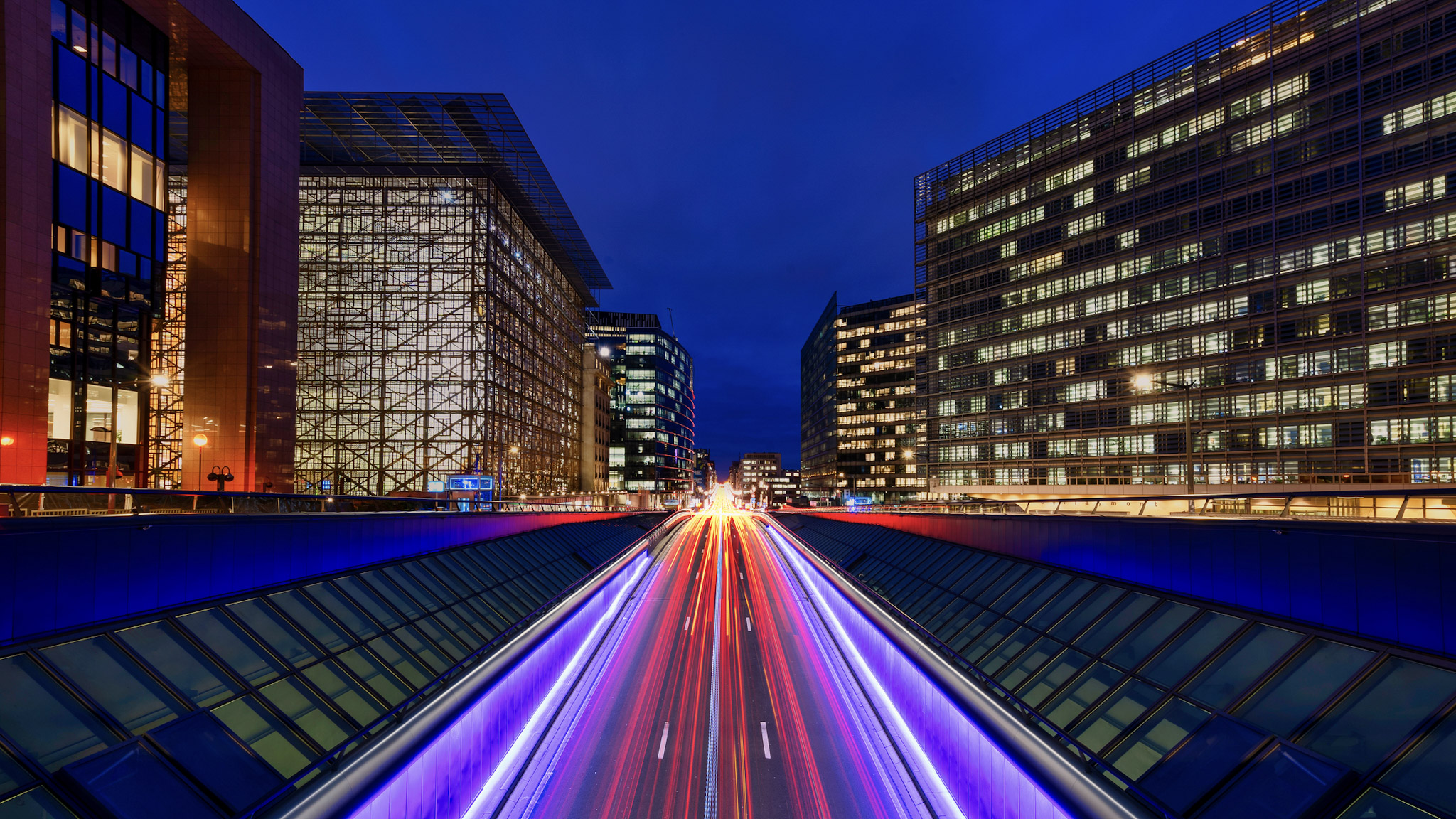
Europe’s Sovereign Cloud Crossroads: Competitiveness vs Control
As the race to advance digital economies gathers pace, European leader...
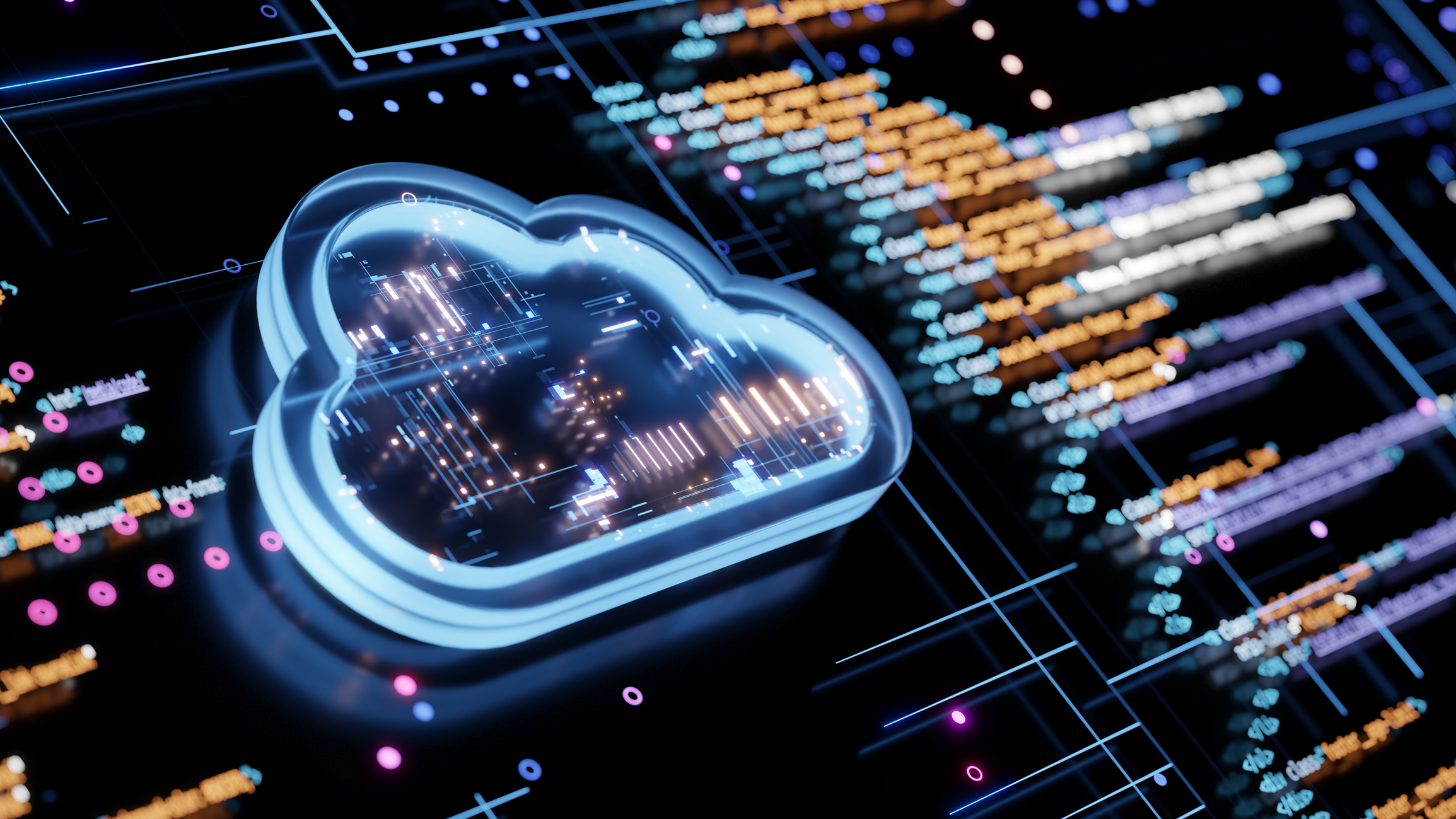
Broadcom’s Private Cloud Outlook 2025 Report Reveals Definitive Cloud Reset
Private clouds are no longer playing catch-up, and public clouds are n...
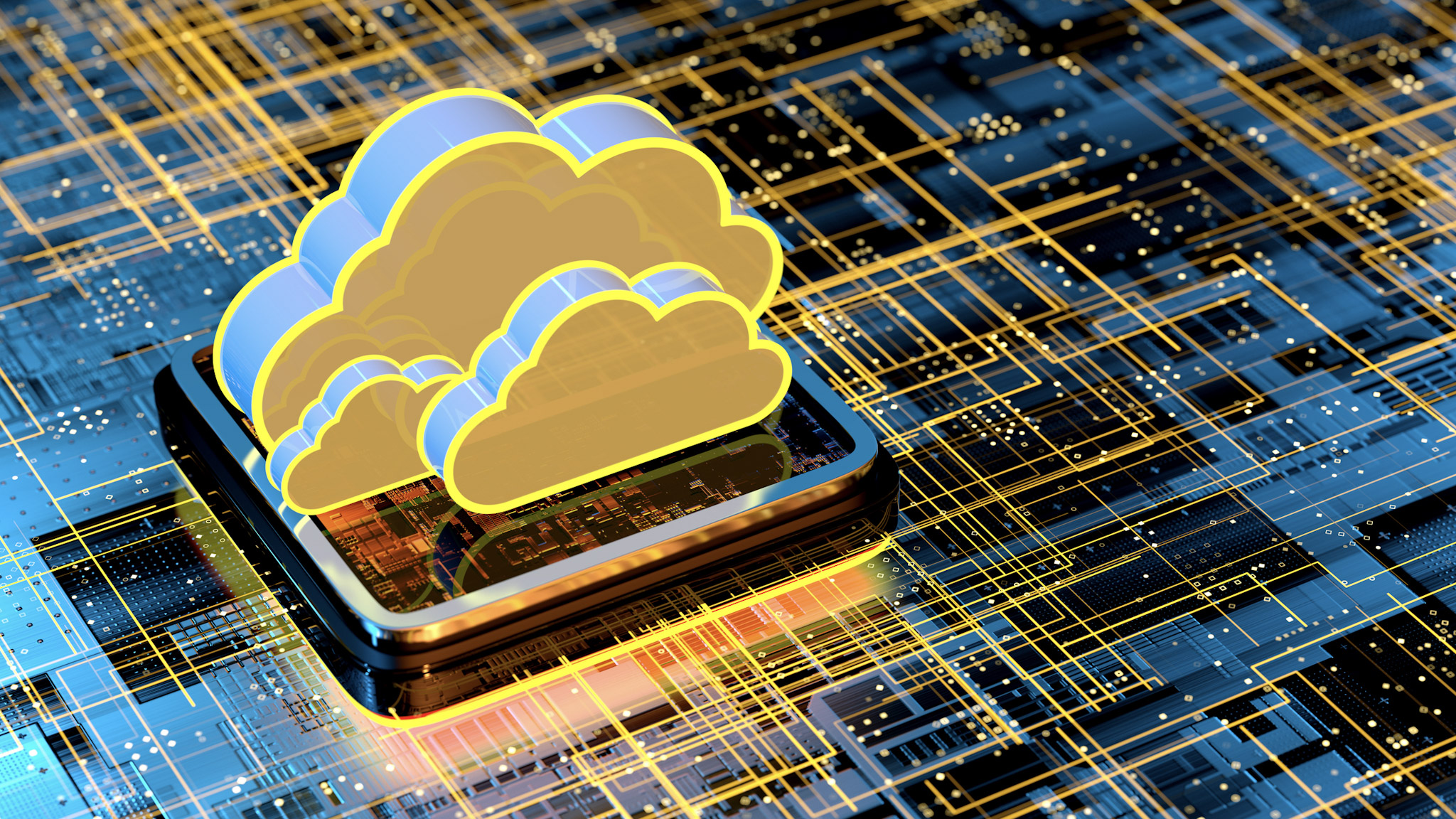
Raising the Bar on Private Cloud – Announcing VMware Cloud Foundation 9.0
When we formed the VMware Cloud Foundation (VCF) Division in Broadcom,...
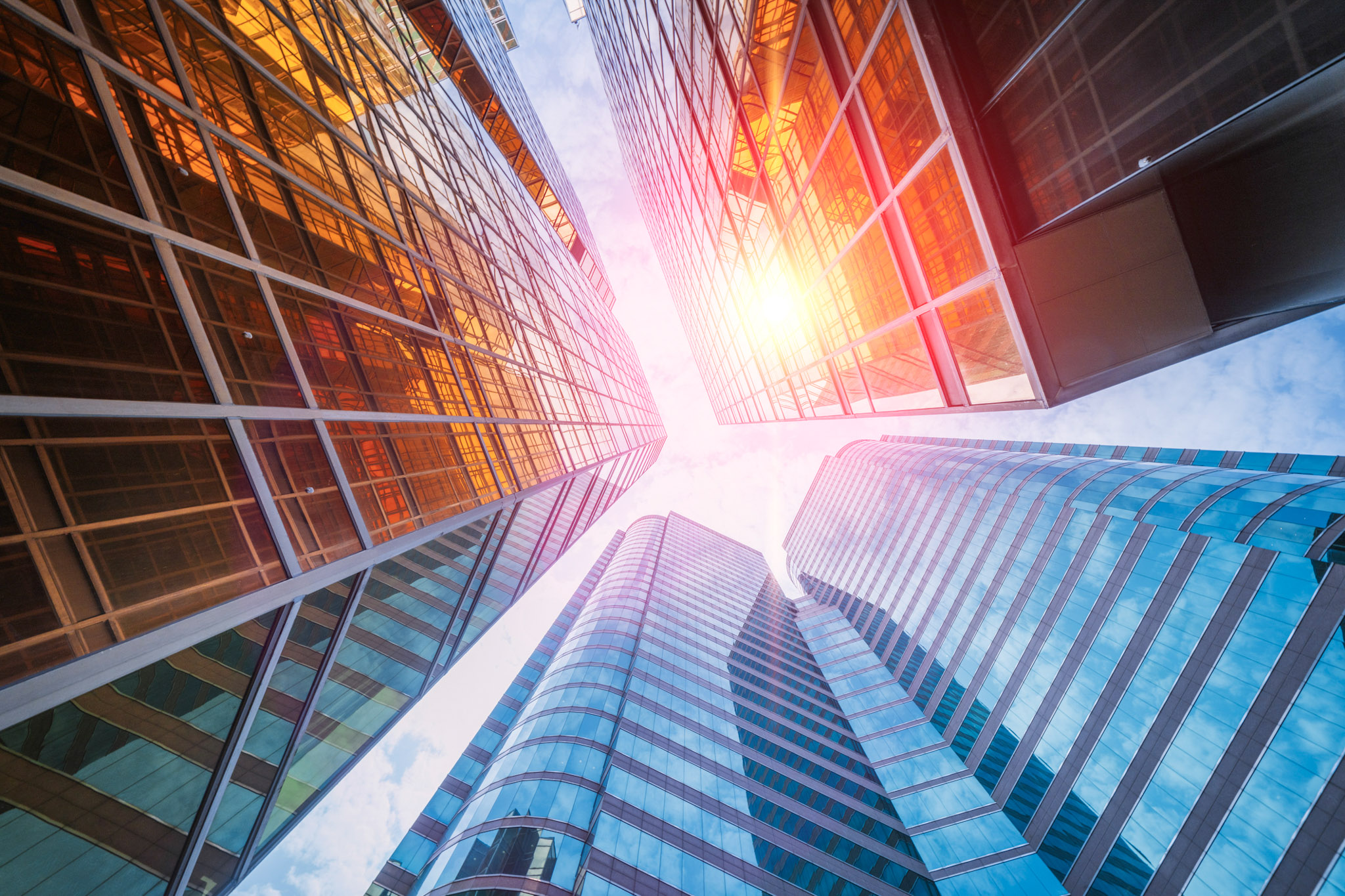
How Arvato Systems Used VMware Cloud Foundation to Deliver a Sovereign Cloud Solution for kubus IT
Across Europe, the Middle East, and select regions in Asia Pacific, or...